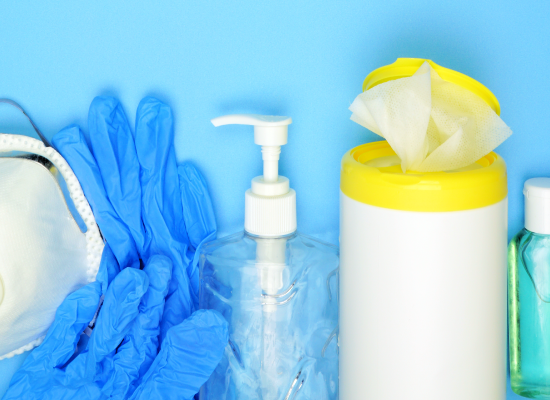
Personal protective equipment (PPE) is worn to minimize exposure to hazards that cause serious workplace injuries and illnesses. These injuries and illnesses may result from contact with chemical, radiological, physical, electrical, mechanical, or other workplace hazards. PPE may include items such as gloves, safety glasses and shoes, earplugs or muffs, hard hats, respirators, or coveralls, vests and full body suits.
To ensure proper use of PPE, all equipment should be:
- Safely designed and constructed
- Maintained in a clean and reliable fashion
- Comfortable, encouraging worker use
If the PPE does not fit properly, it can make the difference between being safely covered or dangerously exposed.
Workers Have the Right to:
- Working conditions that do not pose a risk of serious harm.
- Receive information and training (in a language and vocabulary the worker understands) about workplace hazards, methods to prevent them, and the OSHA standards that apply to their workplace.
- Review records of work-related injuries and illnesses.
- File a complaint asking OSHA to inspect their workplace if they believe there is a serious hazard or that their employer is not following OSHA's rules. OSHA will keep all identities confidential.
- Exercise their rights under the law without retaliation, including reporting an injury or raising health and safety concerns with their employer or OSHA. If a worker has been retaliated against for using their rights, they must file a complaint with OSHA as soon as possible, but no later than 30 days.
Employers must provide personal protective equipment to their workers and ensure its proper use. Employers are also required to train each worker required to use personal protective equipment to know:
- When it is necessary
- What kind is necessary
- How to properly put it on, adjust, wear and remove it
- The limitations of the equipment
- Proper care, maintenance, useful life, and disposal of the equipment
If PPE is to be used, a PPE program should be implemented. This program should address the hazards present; the selection, maintenance, and use of PPE; the training of employees; and monitoring of the program to ensure its ongoing effectiveness.
Water, Rest, Shade
During the hot summer months, heat stress is a real issue for those working outside for extended periods or those in a non-air conditioned building. PPE for these environments can include water- or air-cooled clothing, and cooling vests.
Heat-related illness is preventable. Workers who have not spent time recently in warm or hot environments and/or being physically active will need time to build tolerance to the heat. During their first few days in warm or hot environments, employers should encourage workers to:
- Consume adequate fluids (water and sport drinks),
- work shorter shifts,
- take frequent breaks, and
- quickly identify any heat illness symptoms.
Engineering controls such as air conditioning with cooled air and increased air flow can make the workplace safer.
Other options for keeping body temperatures down in warm environments include making changes to workload and schedules. For example, slow down physical activity like reducing manual handling speeds or scheduling work for the morning or shorter shifts with frequent rest breaks in the shade or at least away from heat sources.
The difference between a respirator and a facemask
Respirators and facemasks are two types of personal protective equipment that are used to protect workers in healthcare and other settings. A facemask is not a respirator, and that’s an important distinction to understand.
What is a Respirator?
A respirator is a type of PPE designed to reduce exposure to airborne contaminants. Respirators are available in different types and sizes, and the respirator used must be individually selected to fit the face and to provide a tight seal.
A proper seal between the face and the respirator forces inhaled air to be pulled through the respirator’s filter material, and not through gaps between the face and the respirator. If you are required to use a respirator, it must be NIOSH-certified and must be used in the context of a comprehensive respiratory protection program, according to OSHA’s Respiratory Protection standard, which includes but is not limited to medical evaluation, fit testing, and training elements.
Respirators are used routinely to protect healthcare workers against airborne infectious diseases, such as tuberculosis, anthrax, SARs, and Hantavirus because they protect against both large and small particles.
What is a Facemask?
A facemask is a loose-fitting, disposable mask that covers the nose and mouth. Surgical masks, dental masks, medical procedure masks, isolation masks and laser masks are all types of facemasks. Facemasks help stop large droplets from being spread by the person wearing them. Facemasks also keep splashes or sprays from reaching the mouth and nose of the person wearing them. However, facemasks are not designed or certified to seal tightly against the face or to prevent the inhalation of small airborne contaminants.
During inhalation, small airborne contaminants pass through gaps between the face and the facemask and the material of the mask. Remember, facemasks are not considered respirators and they do not provide respiratory protection. Only facemasks that are cleared by the U.S. Food and Drug Administration (FDA), may be legally marketed in the United States. The FDA approval signifies that they have been tested for their ability to resist splashes of blood and other body fluids.
To offer protection, both facemasks and respirators need to be worn correctly and consistently throughout the time that they are being used. When used properly, facemasks and respirators both play an important role in preventing exposures to different types of hazards.
During an infectious disease outbreak, such as SARs or pandemic flu, facemasks and respirators should be used in conjunction with other controls and interventions that are known to prevent the spread of infection. These include engineering and administrative controls, such as installing sneeze guards and permitting teleworking, and work practices, such as cough etiquette, hand hygiene, and avoiding large gatherings.
Ten Steps All Workplaces Can Take to Reduce Risk of Exposure to COVID-19
- Encourage workers to stay home if sick.
- Encourage respiratory etiquette, including covering coughs and sneezes.
- Provide a place to wash hands or alcohol-based hand rubs containing at least 60% alcohol.
- Limit worksite access to only essential workers, if possible.
- Establish flexible worksites (e.g., telecommuting) and flexible work hours (e.g., staggered shifts), if feasible.
- Discourage workers from using other workers’ phones, desks, or other work tools and equipment.
- Regularly clean and disinfect surfaces, equipment, and other elements of the work environment.
- Use Environmental Protection Agency (EPA)-approved cleaning chemicals with label claims against the coronavirus.
- Follow the manufacturer’s instructions for use of all cleaning and disinfection products.
- Encourage workers to report any safety and health concerns.
Sources: OSHA, NIOSH