Prevent Workplace Accidents with a Hazards Assessment
Baldwin & Lyons requires its workers’ compensation policyholders to establish a safety and health policy statement declaring that their company will institute and administer a comprehensive and continuous injury and illness prevention program for workers. Before you can establish a safety and health policy, you must identify the hazards and assess the risks associated with the dangers that exist in your specific workplace.
Hazards are created by physical, biological and chemical environmental conditions; equipment and materials; and management practices, including insufficient budget allocations, inadequate training, and too little emphasis on safety and health issues.
Senior management should help implement all safety programs to emphasize the value your company places on safety. Adequate resources must be provided for safety programs, and senior management should be involved whenever results are reviewed and evaluated. Incorporating the Occupational Safety and Health Administration’s (OSHA) compliance guidelines into your job hazard analysis will help ensure that your health and safety program meets federal standards. In addition, an effective workplace hazards assessment will keep your workers safer, reducing accidents, lost time and production due to injuries, and damages to your facility, materials and equipment.
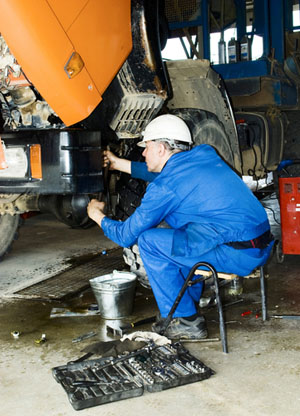
Employers must certify in writing that their company has performed a workplace hazards assessment. To get started, you should first identify hazards by analyzing all workers’ tasks. Involve your workers in the identification of risks. They have a unique understanding of their jobs, which will help you minimize oversights and ensure a high-quality analysis.
Inspect work areas and equipment, and review prior accidents, occupational illnesses, losses and near misses. These events indicate areas in which existing hazard controls may not be adequate. If this is the case, make recommendations to improve the current controls.
Identify the people, property and environments that could be harmed or damaged by the hazards you recognize. Audit the safety programs and management systems that your company already has in place. If new hazards are identified, or if they are not being properly addressed, make adjustments in order to prevent and mitigate losses and exposures. If you make changes to your safety policy, inform and train your workers of the new procedures or practices.
Through the process of analyzing workplace hazards, you should be able to predict fatalities, injuries, property damage and other consequences that could result. Determine the severity of these exposures and the likelihood they will occur. Based on what you conclude, rank and set priorities for addressing hazardous jobs. Those that present the most immediate or severe risks should be your top priority. Address them immediately.
Designate an individual to be responsible for the implementation and maintenance of the program. Your workplace hazards assessment should be reviewed and revised any time there are changes to work procedures, changes in operations or equipment, or it becomes known that hazards were overlooked in the layout or design of your facility. By adopting a proactive approach to safety, you can prevent problems from developing in the first place.
{ back } |